
According to the relevant laws and regulations of various countries to manage dry heat sterilization requirements, we should manage them in daily production. The management points are as follows:
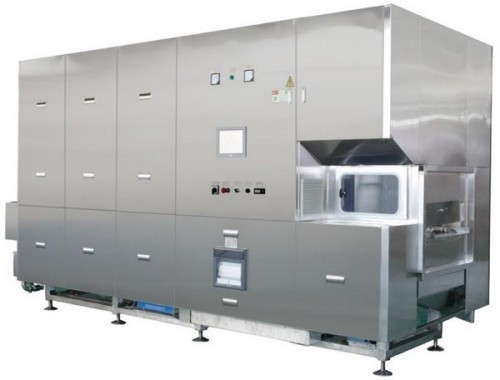
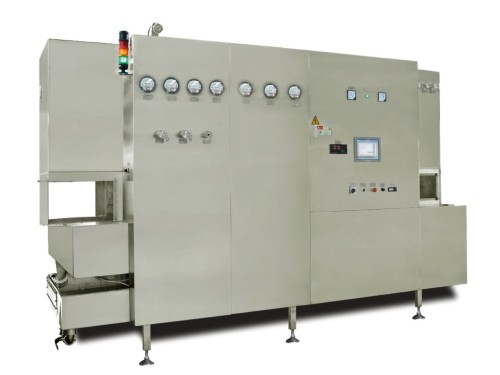
1. In the verification process
(1) Confirmation of electrical components and equipment parts
Availability of alarm when the temperature is below the sterilization/thermogenic removal temperature. Confirm the program controller. Gasket sealing ensures that the sealing of different functional areas in the equipment meet requirements. Air balance is achieved by adjusting baffle/connecting rod. Confirm that the air inside the chamber circulates in a certain airflow direction and speed, and alarm when the laminar flow fan wind speed is lower than the specified value. Confirm that the vibration of the damper regulator is at a minimum value during each sterilization process. Air balance is achieved by confirming that the sterilization chamber is at positive pressure through differential pressure, preventing non-clean air from entering the chamber from outside the equipment. Confirm that all heating elements, conveyor speed and conveyor speed recorder are operating properly. If there is an abnormal transmission speed, can the alarm be activated.
(2) Filter integrity testing
The air outlet system of the dry heat sterilizer must meet the standard of Class A clean air, so the integrity test (e.g. PAO test) of the high efficiency particular air filter should be conducted regularly. The high efficiency particular air filter itself may be damaged by high temperature and generate suspended particles, and the speed of heating up and cooling down during use also have a great impact on the life of the high efficiency particular air filter, so the sterilization procedure must be designed and controlled in strict accordance with the specified speed range of heating up and cooling down by the supplier.
(3) No-load heat distribution test
No-load heat distribution test is a test to confirm the temperature uniformity and the "cold spot" of the equipment at no-load, and is usually performed during operational confirmation. The temperature of different parts of the sterilizer chamber is determined by a set of calibrated temperature sensors and the temperature distribution graph is plotted based on the determined data to facilitate the detection of cold and hot spot in the sterilization chamber. At least 10 temperature sensors are used during the testing of sterile items. The sensors should not be installed in contact with metal (e.g. internal walls, etc.) inside the chamber and at least one sensor should be set near the temperature sensor of the device's own control system during the test.
Under normal conditions, the error between the temperature value and the set value at each point in the chamber should be within the range specified in the validation program, as USP <1211 > states that for dry heat sterilization and heat removal systems operating above 250°C, the acceptable qualified range for the no-load heat distribution in the sterilization chamber is ±15°C. This test should be performed three times consecutively to demonstrate the reproducibility of the heat distribution. The test conditions should be consistent with conditions during the production process, such as ambient temperature, relative humidity, and air pressure balance in the operation area. Record the entire temperature change process, including the heating and cooling process. Deviations in the time of heating and cooling help to detect equipment failures during the sterilization process. If the temperature distribution does not meet the standard in the test, the sterilizer should be adjusted or repaired, usually by adjusting the air inlet, the induction and recirculation air baffles to improve airflow.
Heat penetration test and full load heat distribution heat penetration test should usually be performed on materials with representative specifications and types. For tunnel ovens, the conveyor speed should be increased and the set temperature should be decreased as much as possible. In addition to materials that are difficult to penetrate (such as tightly bundled materials), representative loading also include minimum and maximum loading. Due to the poor thermal conductivity of air, cold and hot spot in different sterilized items may change. Hot and cold spot variations may occur if each material is heated at a different speed. Heat penetration and heat distribution should be monitored simultaneously. Recording the changed speed of air and sterilized objects in heating and cooling is important during the test.
The temperature sensor indicating the heat distribution illustrates the time required for the air temperature to reach the sterilization temperature setting under loading conditions, while the temperature sensor for the heat penetration test reflects the time required for the sterilization object to reach the sterilization exposure temperature. Obviously, the time for the sterilization object to reach the minimum sterilization temperature will lag behind the time of the hot air in the chamber to reach the minimum sterilization temperature, and the lag value is the most pronounced at maximum loading. In order to ensure that the sterilized object can be exposed to the sterilization temperature for a long enough time, the temperature setting of the sterilizer control system is often higher than the minimum temperature required for the sterilization and heat removal process, and the entire time that the product is exposed to the minimum sterilization temperature and the accumulated Fh value should be recorded in the validation document. If several "cold spot" are found in the heat distribution and heat penetration tests during the sterilization process of containers (e.g., vail). In subsequent tests, there should be sufficient temperature sensors to monitor the vail or other containers in the area of the "cold spot". When the heat distribution and heat penetration tests meet the criteria specified in the design and validation program, the sterilizer should be run three times continuously to demonstrate the reproducibility of the sterilization and heat removal process. In the repeat test, a certain number of temperature sensors must be placed centrally in the "cold spot" area to prove that the minimum Fh value in the "cold spot" area meets the specified requirements.
(4) Microorganism challenging experiments
Bactericidal should be confirmed by a microorganism or endotoxin challenge test, which can be performed simultaneously with thermal penetration or independently. For sterilization technology validation, the bioindicator can be placed at each cold point (with the lowest Fh value) for testing; the coldest spot and the most value placed in the load can also be selected, i.e. the worst condition case. Usually Bacillus subtilis black variant spore is selected for testing at a concentration of 106 spore/point. For the validation of the heat removal technology, bioindicators are generally selected Escherichia coli endotoxin for testing, i.e., bacterial endotoxin inactivation test. In the period of endotoxin inactivation validation, samples should be placed in the area with the worst loading conditions (usually maximum loading) and slowest temperature rise, 2 samples per point, and one probe should be placed near the worst point. Since the technology conditions for heat removal are much harsher than the sterilization technology conditions for killing spores, it is not necessary to perform bioindicator challenge tests when implementing endotoxin challenge tests in dry heat sterilization technology validation. The endotoxin challenge reagents for heat removal validation can use purchased directly endotoxin challenge test tubes or, depending on the situation, home-made endotoxin challenge test standards, but all reagents need to review the endotoxin labeled amount before testing.
2. In the daily production process
After the hot air circulation tunnel oven is validated, the operation of the sterilization procedure is continuously monitored during the production process to confirm that key parameters are within the validation range, such as temperature, belt speed, pressure, differential pressure, etc. Deviation investigation and change control should be performed when key parameters are out of the validation range, and preventive maintenance should be set to ensure that the sterilization technology remains under control.
Regular assessment and reconfirmation, including high efficiency particulate air filter leak test; regular environmental monitoring according to risk assessment, monitoring frequency according to process requirements and monitoring of upstream and downstream pressure difference of high efficiency particular air filter; determination of high efficiency particular air filter replacement cycle according to wind pressure and environmental monitoring, etc.
Physical data monitored during the daily production process include: transfer speed, temperature of each area section, monitoring of upstream and downstream differential pressure of high efficiency particulate air filter, system alarms for deviations from technology parameters, and handling measures.
In the daily production process, attention should be paid to the replacement of equipment components, such as the replacement of high-efficiency particulate air filter and fan, and pay attention to the installation direction to avoid reverse installation; timely clean glass chip collection box; lubricate and maintain the fan, etc.
Measurement instruments of equipment should be regularly calibrated in order to monitor the operation and use of equipment status. In addition, to ensure that the validation equipment can be well maintained, operators need to be trained through a good training system to ensures that operators can follow standard operating procedures to carry out production and equipment usage processes.